Fuel Injector 127-8222 127-8216 127-8205 0r-8682 0r-8461 for Caterpillar 3116 3114 Engine
products detail
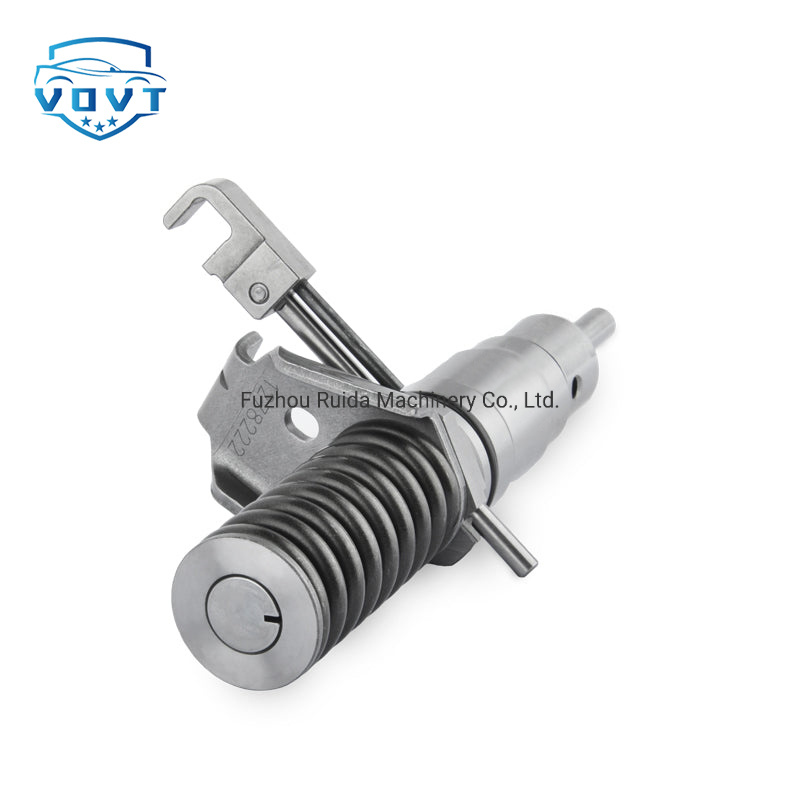
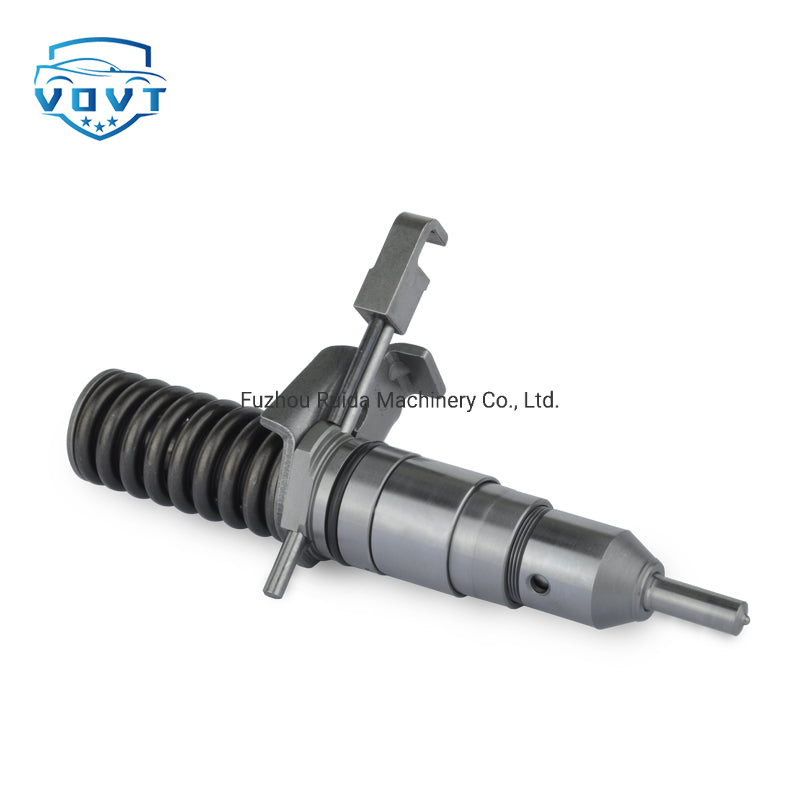
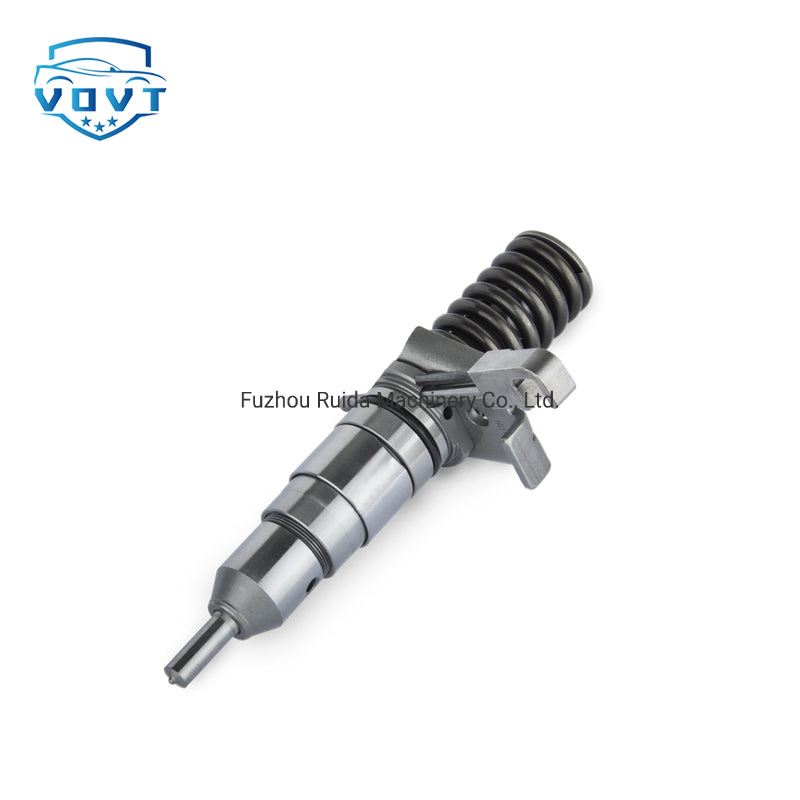
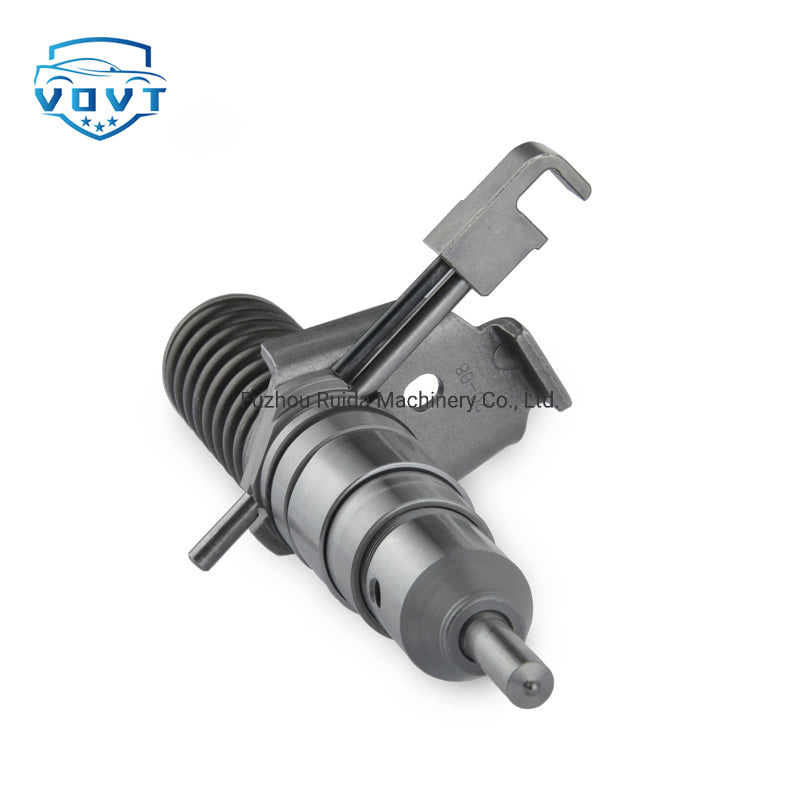
Used in Vehicles / Engines
Product Code | 127-8222 127-8216 127-8205 0R-8682 0R-8461 |
Engine ModelCB-634 CB-634C | CB-634 CB-634C CB-634D CP-533 CP-533C CP-533D CP-563 CP-563C CP-563D CS-531 CS-531C CS-531D CS-533 CS-533C CS-533D CS-563 CS-563C CS-563D CS-573C CS-573D CS-583 CS-583C CS-583D IT24F IT28G IT38F IT38G 924F 928G 938F 938G 950F 613C 446B 446D D5M D6M AP-1000 AP-1000B AP-1050B AP-1055B AP-900B BG-240C BG-2455C BG-245C BG-260C 561M M320 M325B 953C 963B 963C |
Application |
Caterpillar Brand
|
MOQ | 6 pcs / Negotiated |
Packaging | White Box Packaging or Customer's Requirement |
Warranty | 6 months |
Lead time | 7-15 working days after confirm order |
Payment | T/T, PAYPAL, as your preference |
FAQ
Cavitation Inside High-Pressure Optically Transparent Fuel Injector Nozzles (PART 3)
How the device was sealed, and how the plates were held in place, was not included in the published results. Two forms of string cavitation were observed: one which formed in the vortices attached to the part of the geometry designed to mimic the needle, and another which formed in a vortex that connected two orifice holes.
Badock et al. achieved elevated injection pressures using acrylic nozzles, although much like Arcoumanis et al, the piece was significantly larger than the original injector nozzle[4]. Studying primary breakup of a spray in such a nozzle is impossible due to the lensing effect of the surface of the drilled reliefs which fix the length of the nozzle orifice passages.
Blessing et al. achieved injection pressures of 800 bar using an acrylic injector nozzle with a single off-axis orifice[5]. The design was compact enough to allow the primary breakup of the spray emitting from the nozzle orifice to be studied simultaneously with the in-nozzle orifice cavitation.
Unfortunately, no further information regarding the design, such as dimensions or sealing mechanism, was provided. Another effort which deserves mention is the recent study by Butcher et al[6]. The group constructed a quartz nozzle in order to study flash boiling sprays relevant to spark-ignition engines and even installed a modified needle to reduce the stress concentration in the nozzle from the force of the needle seating. Their injection pressures were limited to 40 bar.
The most recent study that achieved elevated injection pressures is that of Mitroglou et al[7]. The authors examined the cavitation structures inside an optically transparent VCO geometry with six orifice holes. They reached 400 bar, but due to slow flaw growth and the desire to collect enough data to build ensemble averaged images of cavitation structures, the injection pressure was limited to 300 bar. Cavitation was observed on both sides of the orifice, as in the earlier study of Arcoumanis. In this study, string cavitation was observed only during the opening phase of the needle valve, and corresponded to the location of a vortex attached to the injector needle face.